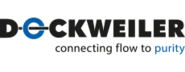
Dockweiler Japan Co., Ltd.
Hikawazaka Bldg. 2F
6-8-9 Akasaka
Minato-ku, Tokyo
107-0052
Japan
Products used in the semiconductor industry must be manufactured in a high purity environment. Any contamination by foreign particles or residues must be avoided. Such conditions only exist in a cleanroom. High purity products such as manifolds or process vessels are welded, assembled, tested and packaged in a cleanroom.
We bear responsibility for the highest purity of our products. I am fully aware of that.
Our UHP manifold systems meet all requirements of the semiconductor industry. The prefabricated manifolds are collared and then welded, tested and packaged in a Class 10 cleanroom.
They are made-to-order solutions for the semiconductor industry. With orbital welds and a 100% helium leak test (leakage rate of 1 x 10⁻⁹ mbar l s⁻¹), they offer maximum process reliability for your plant.
Further information or a personal consultation? Our products and know-how are there to provide solutions.